True Velocity Ammo: The Future Is Now, Old Man
At RECOIL, we review every product fairly and without bias. Making a purchase through one of our links may earn us a small commission, and helps support independent gun reviews. Read our affiliate policy.
Find out more about how we test products.
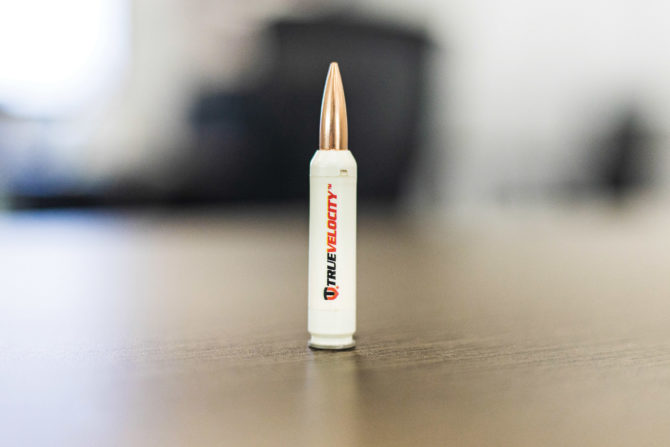
As I finish up the copy for this article, painstakingly written in longhand for my typesetter to layout on the Linotype machine, I’m contemplating hitching up the old horse and buggy to take a trip down to the telegraph office to let my team know of the wonders of the technological age that is soon to be upon us.
Can you think of any other realm of human endeavor that’s still stuck in the late 19th century? Me neither.
The firearm industry can charitably be described as a mature technology. There’s a case to be made that the last time we really saw game-changing innovation was when Borchardt first managed to make a handgun load metallic cartridges from a magazine. In 1893.
Since then, manufacturers have pretty much stuck to the same old tune, with brief-lived excursions into evolutionary dead-ends such as the Gyrojet: After all, why change something that ain’t broke? Which is why we don’t have laptops or smartphones, or basic family sedans that’ll top a buck-fifty. Oh wait, we do. So why the blue f@ck are we still using guns and ammo from the second Cleveland administration?
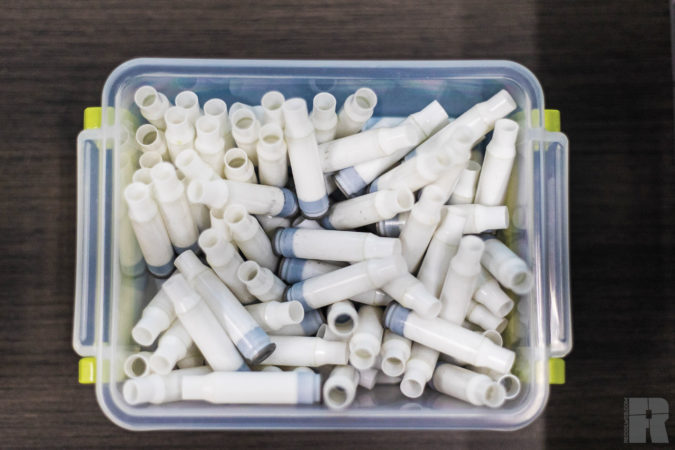
True Velocity is trying to drag the ammo industry into the 1960s through the use of composite cases, but they may well end up overshooting that goal. Here’s why.
Visit any major ammo plant in the U.S. and you’ll find equipment producing brass cases, using a process that hasn’t changed much since the Victorian era, though in some instances the machinery might be a little newer. Like, 1940s newer. To make a case, a slug of brass is punched out of a strip to form a cup, which is then progressively formed by poking it with a succession of presses to form a close-ended tube. This tube is then smashed against a die to form the case head, turned in a lathe to cut the extractor groove, and squashed by another set of dies to form the shoulder and neck. Between each stage, the case must be annealed or softened by heating, as well as washed and lubricated. It’s a complicated, messy, and violent process, and it’s no coincidence that identical, match-grade cases are expensive and difficult to make. Producing consistent wall thickness — and hence uniform internal volume — is the bane of process engineers, requiring high-grade raw materials, constant attention to detail, and shortened tool life.
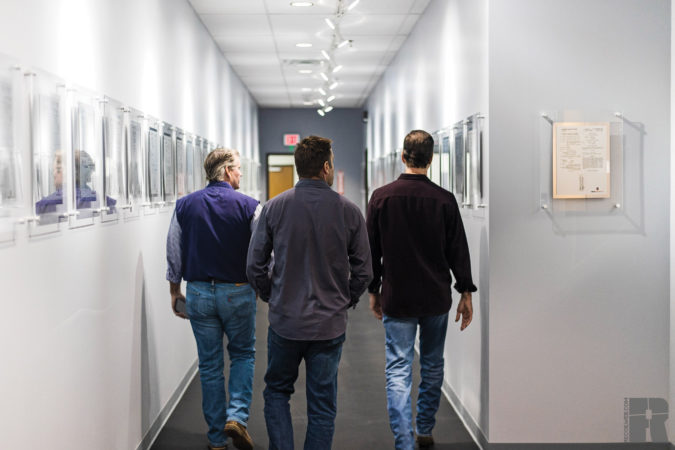
There are certain restrictions placed on case design, due to both the material used and the manufacturing process. For example, because brass is formed using punches, the internal shape must have straight walls (or a taper toward the mouth), otherwise the punch would get stuck. Bullets are held in place and guided into the rifling by the case neck, which has to be a certain length — too short and setback will occur, too long and you’re just wasting material and space. When you’re on the shop floor of a cartridge-forming facility, the process looks, sounds, and smells like a product of the industrial revolution, which it is.
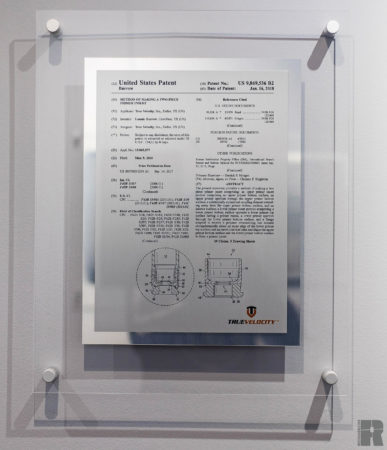
I’ve worked in production shops, run CNC machines, and love the smell of cutting oil, so when I visited the factory floor in True Velocity’s Garland, Texas, facility, I was a little taken aback. Machinery quietly hums along, the place is spotless and gleamingly bright, reminiscent more of a pharmaceutical plant than a dark satanic mill. The process of polymer case production stands in stark contrast to its brass counterpart, and the aroma of oil and detergent is replaced with a faint whiff of melted plastic.
Making a composite case is a three-step process. Case heads are turned on CNC screw machines from precipitation-hardened stainless steel, and at present are produced off-site by a small group of subcontractors. The company has plans to bring some of this in-house, but spreading the load among the local industrial base makes sound business sense, as it’s able to ramp up faster should demand spike every four years as it has for the past three decades.
There are other advantages to be gained from the use of a turned, stainless case head. Ever had a case let go due to an overpressure event? Shoot enough long enough and it’ll happen, and the first thing you’ll notice after changing your shorts is that there’s a consistent pattern to these failures. The most common is that the case will let go just forward of the extractor groove, blowing out fragments where bolt and chamber leave a bit of brass unsupported by steel. The yield strength of brass is around 23K psi, while 17-4 stainless is at least three times this, depending on heat treat, which gives a substantial safety margin. There’s also way more freedom to design the internal geometry of the case head, optimizing its shape in order to promote both propagation of the primer’s flame front and the subsequent burn of the propellant.
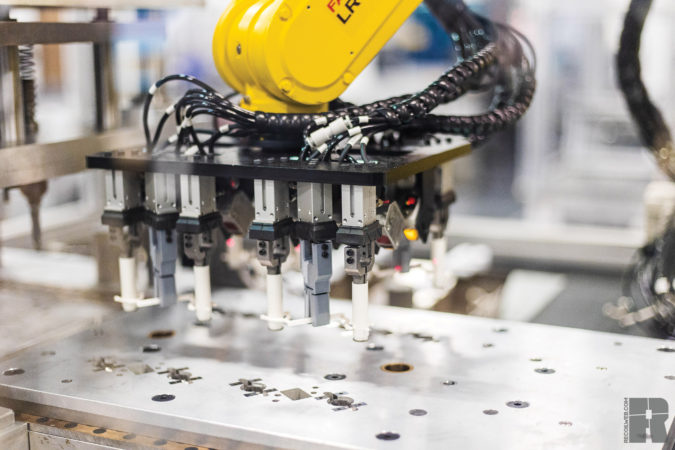
In order to continue its journey through the plant, the case head is mated to a two-piece polymer body, the lower half of which is injection molded through the flash hole, while the neck and shoulder are added in a separate operation. This is one of the 110 or so patents held by True Velocity, which has spent the past decade refining composite case production to the point where they’re in a similar position to Apple — you can be a competitor making something in the same field, but they’re getting paid no matter what, as the IP is pretty much sewn up.
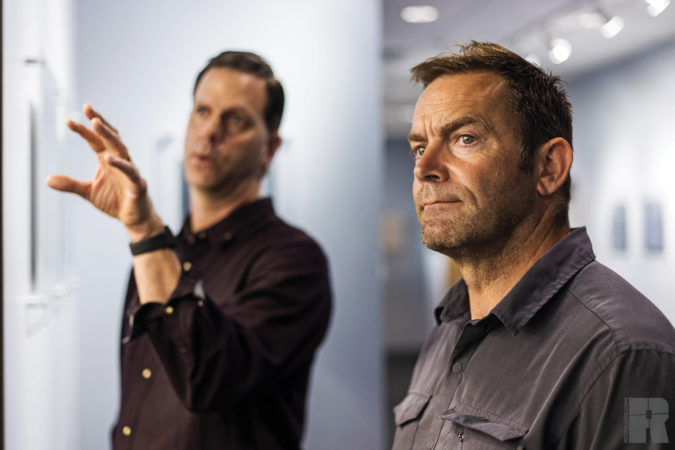
By injection molding the case body, tweaks can be made to its internal shape, as it’s not dependent on being formed by a punch. If you look at a cross section of True Velocity’s 6.8 round, it’s reminiscent of the combustion chamber of a rocket motor rather than a straight-walled tube, and the company claims it’s able to wring 10- to 15-
percent greater performance from a given charge as a result.
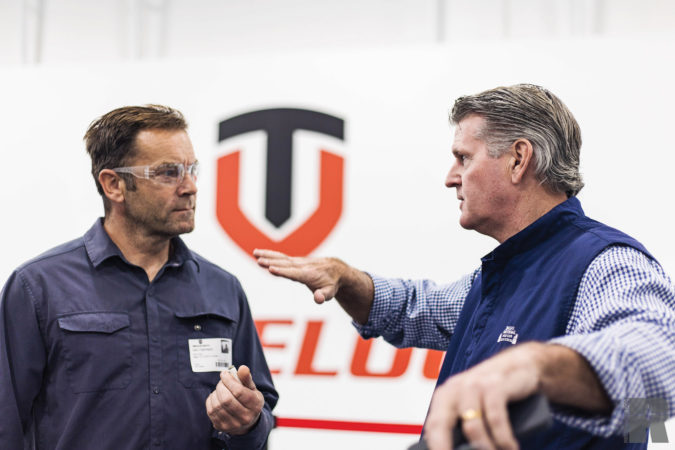
If you’ve ever prepped brass cases for a PRS match, you’ll no doubt have spent time inspecting and then uniforming flash holes, as getting a consistent start to the ignition process is one of the key steps in achieving low SDs when it comes to velocity. Sometimes, the punch creating the hole through which the primer’s energy is directed wanders off course, or there’s a burr left inside the case that must be chamfered in order to avoid an off-center flame. True Velocity addresses this issue in a different way.

Due to their manufacturing process, the flash hole is oversized compared to conventional cases, so that excess diameter is throttled back by means of a tiny brass washer, a couple of thousandths of an inch thick. Each one is placed into the primer pocket and then visually inspected for defects. 100-percent inspection is generally avoided in manufacturing, especially when it comes to mass production, as the costs involved are prohibitive; plus, would you want to spend your life examining tiny brass washers, day in, day out? It’s a pretty good recipe for a serious substance abuse habit. Instead of using humans, a hi-res camera linked to a computer does the dirty work of kicking out anything that doesn’t look perfect. True Velocity states their cases aren’t reloadable, and we suspect that this tiny washer is one of the reasons why — though given the nature of the firearms aftermarket, maybe someone will come up with a solution in the not-too-distant future.
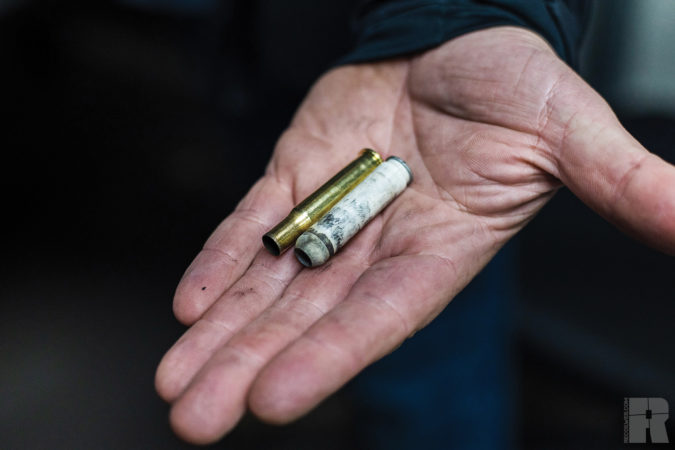
In addition to consistency and velocity advantages, polymer brings another couple of benefits to the table. Weight is reduced by a factor of 30 percent, meaning that a warfighter’s basic combat load of 210 rounds of 5.56 drops to 3.9 pounds from 5.6. Of course, no one looks at things that way, so instead think of it as being able to carry 300 rounds for the same weight. Mo’ bullets, mo’ better.
That same benefit of weight reduction applies in spades when applied to crew-served weapons, or those fitted to aircraft. Take, for example, the 6,000 rounds of 7.62 used to feed the M134D miniguns found on little birds. Exchanging about 100 pounds of brass for an equivalent weight of JP8 means the airframe can loiter for 30 additional minutes on station, providing overwatch while troops are on the ground.
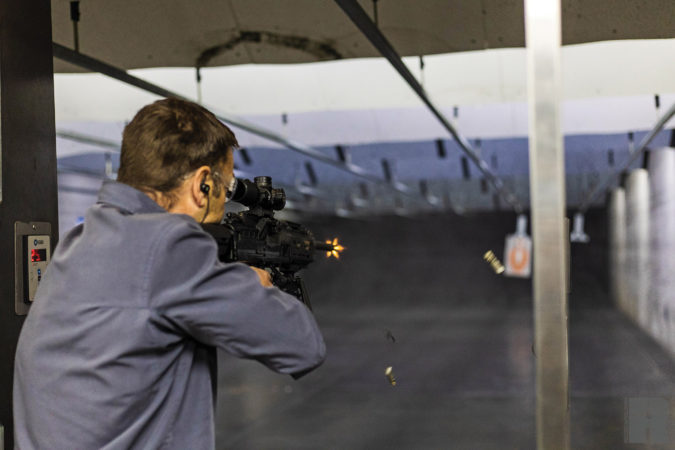
Next to politicians, heat is perhaps the biggest enemy of firearms. As steel and aluminum get hotter, their strength and resistance to wear become compromised, resulting in barrels being shot out, bolts breaking, and gas ports eroding. What has come to be regarded as an inevitable part of the firing process, doesn’t necessarily have to be that way. One aspect of the physical properties of brass, namely its conductivity, has always been touted as a benefit, acting as a heat sink to remove energy from the system when it’s ejected. It turns out that this might not quite be true. Instead, that very conductivity results in heat being transferred to parts of the gun we’d really rather keep cool, and, in this respect, polymer has an advantage of being an insulator.
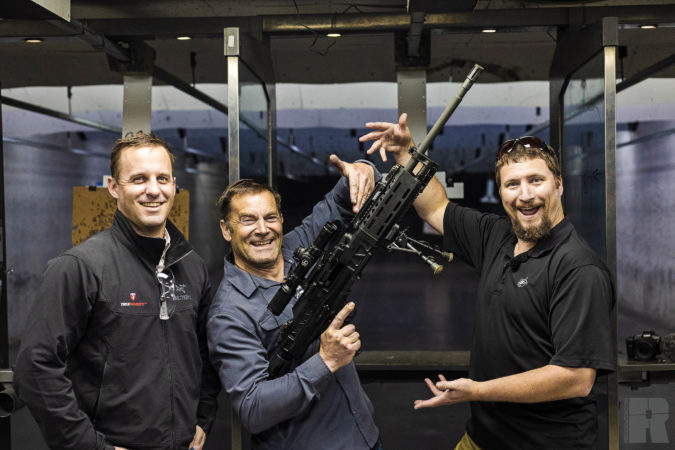
On the macro level, using all the energy contained within the propellant charge to send a projectile on its merry way makes a lot more sense than using it to heat up critical parts of the gun. On a personal level, not doing the hot brass salsa when you get a case down your shirt is a bonus.
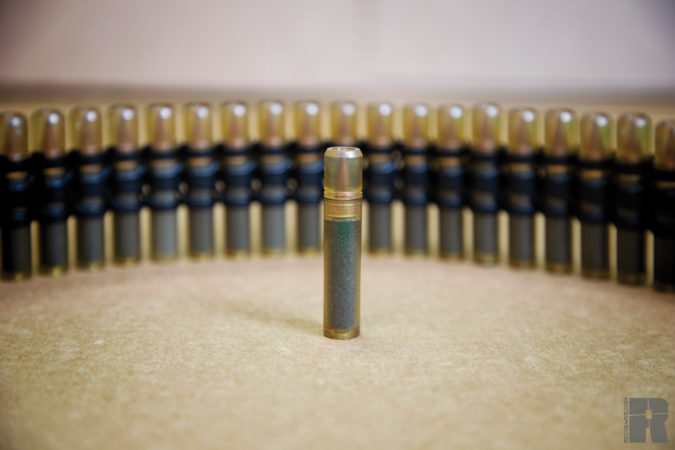
6.8 TVCM vs The Rest
Born of the Army’s quest for a rifle and machine gun that’d allow infantrymen to punch through the latest body armor fielded by our near-peer adversaries, the 6.8 TVCM round fired from a General Dynamics bullpup currently has two rivals from SIG and Textron.
All three take different approaches to solving big green’s request, which in a radical departure from most small arms procurement procedures might actually end up with something worthwhile. Rather than giving the companies a cartridge and telling them to go design something around it, the Army gave a ballistic requirement and let the boffins do their thing. That requirement was to launch a 140-grain .277 penetrator projectile at 3,000 fps from a 16-inch barrel — how it ended up there was pretty much up to the engineers.
SIG’s solution is perhaps closest to existing small arms design, which in the individual weapon uses a beefed-up version of the MCX rifle, chambered in their proprietary .277 Fury cartridge (and please don’t refer to it as the 277 Furry — they get sniffy). In order to handle chamber pressures running at around 80K psi, like True Velocity, the case uses a stainless steel head mated to a brass body.
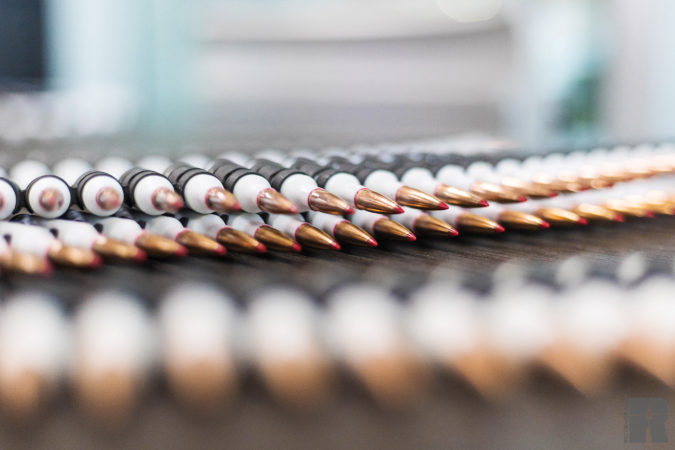
The most advanced in terms of architecture and execution is Textron’s employment of a cased-telescoped munition in a weapons system they developed in conjunction with H&K. By enclosing the projectile completely within a plastic case, overall length is reduced, mags can be smaller and easier to carry, at the expense of a more complicated breech mechanism.
There’s no doubt in our mind that True Velocity’s composite-cased ammo offers some very real and significant benefits over existing brass-cased ammunition, though whether those benefits will be sufficient to overcome market inertia remains to be seen. A quick glance online shows legions of internet mouth-breathers whose only contribution to the advancement of small arms can be found in comments sections where, “I’ll stick with my XYZ, thanks,” is the limit of their genius. If you feel like testing the waters, then sticking a toe into the short-action 270 world isn’t too big of a lift with a bolt gun chambered in 6.8 TVCM, and we suspect it won’t be too long before companies other than KAC will offer it in a large frame AR. The new round handily curb stomps .308 Win and gives a significant velocity advantage over 6.5 Creedmoor, for the same bullet mass. While the benefits of reduced overall weight might not be as important in the civilian world, increased charge efficiency and lower heat transfer to critical parts are universally advantageous.
Whoever ends up being awarded the NGSW contract, the real winners will probably be regular gun owners, as tech spawned by the competition will trickle down to us. Despite the current administration, this may end up being a golden age of firearms development, similar to the latter part of the 19th century. Now, if you’ll excuse me, I have a horse to catch …
Find Out More at tvammo.com
More on Ammunition and The Future of Firearms
- MARS.inc and Cobalt Kenetics's entry into the Military's Next-Generation Squad Weapon Program
- Next-Gen Rifles and SCAR Killers
Why you can trust RECOIL
Since our founding in 2012, RECOIL remains the premier firearms lifestyle publication for the modern shooting enthusiast. We deliver cutting-edge coverage of guns, gear, accessories and technology. We go beyond basic reviews, providing no B.S. buyer’s guides, hands-on testing and expert analysis on everything from firearms and survival equipment to watches and vehicles.
Our reviewers are the backbone of our operation and come from diverse shooting backgrounds: Former law enforcement, military veterans, competitive shooters, seasoned hunters and plain old firearms enthusiasts. Furthermore, we’re not just gun experts, but dedicated journalists who adhere to the strictest standards of our profession.
At RECOIL, editorial independence is the foundation of everything we publish and the cornerstone of reader trust. Our editors, writers and content creators make all editorial decisions independently, free from outside influence. That boils down to: advertisers don’t dictate our coverage, the outcomes of our reviews or what we recommend in our buyer’s guides. First and always, our commitment is to our audience—ensuring every review and article is accurate, unbiased, and driven by real-world experience.
Whether you’re selecting your next firearm, upgrading your gear, or exploring the latest innovations in the shooting world, RECOIL provides the trusted insights you need to make informed decisions. Learn more about our Editorial Standards and how we review products.
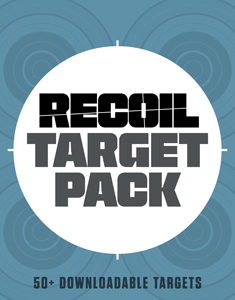
NEXT STEP: Download Your Free Target Pack from RECOIL
For years, RECOIL magazine has treated its readers to a full-size (sometimes full color!) shooting target tucked into each big issue. Now we've compiled over 50 of our most popular targets into this one digital PDF download. From handgun drills to AR-15 practice, these 50+ targets have you covered. Print off as many as you like (ammo not included).Get your pack of 50 Print-at-Home targets when you subscribe to the RECOIL email newsletter. We'll send you weekly updates on guns, gear, industry news, and special offers from leading manufacturers - your guide to the firearms lifestyle.
You want this. Trust Us.
14 Comments
Add a comment
View Comments
-
Every few years a new company comes along that will revolutionize small arms with either caseless or plastic-cased ammo.
-
Great idea, especially for the military with the difference in weight.
So my understanding is that this ammo cannot be reloaded. This puts all shooters at the mercy of the manufacturer. If the government puts restrictions on ammo you'll be stuck with nothing to shoot. At the mercy of the government.
-
Most people DO NOT RELOAD, which means the complaints about that are only affecting less than 10% of todays shooters. If True Velocity can get their ammo to half the cost of traditional ammo then I could car less about reloading. Add in it transfers a substantially less amount of heat to the weapons parts and improves accuracy means its a no brainer. Fudds complaining that this means they cant reload and puts the consumer at the mercy of the gubment forget that commercial 3D printing is far more prevalent in the private sector than in the government sector.
-
"If True Velocity can get their ammo to half the cost of traditional ammo". The issue at the moment is that it costs double what traditional ammo does. $69.99 for 20 rounds of 308? I'll stick with reloadable ammo thank you.
-
Absolutely! The price is ridiculous at the moment.
The article is very snarky about market resistance, but that resistance exists because this is about the 753rd introduction of alternatives to brass cases. From Gyrojet to consumable cases, they've all fallen by the wayside.
Overall, I like the TrueVelocity concept, and I hope it becomes workable. I also like that they're producing calibers like .308, which will allow those of us with conventional firearms to try it out.
But like electric cars, until the price becomes competitive with traditional ammo I'll have to watch the market from the sidelines.
-
-
-
The expensive part of this solution is the machined base insert. Induction heating rod stock should allow die forming an insert to current mass produced brass tolerance. Save the machined parts for sniper duty.
-
Evan though I am an avid reloader, this is the next logical step in ammunition development.
I cant wait to try the two 6.5 Creedmoor
loads. -
As already stated, most don't reload. However, if ammo prices stay high, or stock stays or becomes limited, reloading is always an option. Non-reloadable ammo takes away options. Of course options is why I shoot multiple calibers from different firearms. Bring on the innovation!
-
Is there a time frame on the 6.5 Creedmore ammunition and when it will be available and what weight bullet it will come in. Thanks
-
been keeping an eye out for this stuff for about three years or so , i have lost interest in your company and your product do to the responses ,pricing , and the stupid collector box please remove my email address from your data base
-
The author's snark reminded me about Recoil's early elitist mis-step about "assault weapons." Freedom in America depends now upon us "mouth-breathers," not upon load-bearing prima donnas who actually serve misanthropic globalist banksters and depopulationists. Removing the option of re-loading is not a way to woo support from Americans, but is another way of increasing the divide between us. Keep it up. You'll get the world you deserve.
-
The .gov contracts have covered the R&D cost and we would expect these rounds to cost much less than brass rounds do with the extra savings being passed along to the end users. And if they really want to compete in the commercial market and take a large share then now would be a great time to make that consumer friendly move happen. You can bet that today's shooters would reward them for the good will alone and keep the presses rolling 24/7.
Every few years a new company comes along that will revolutionize small arms with either caseless or plastic-cased ammo.
Great idea, especially for the military with the difference in weight.
So my understanding is that this ammo cannot be reloaded. This puts all shooters at the mercy of the manufacturer. If the government puts restrictions on ammo you’ll be stuck with nothing to shoot. At the mercy of the government.
Most people DO NOT RELOAD, which means the complaints about that are only affecting less than 10% of todays shooters. If True Velocity can get their ammo to half the cost of traditional ammo then I could car less about reloading. Add in it transfers a substantially less amount of heat to the weapons parts and improves accuracy means its a no brainer. Fudds complaining that this means they cant reload and puts the consumer at the mercy of the gubment forget that commercial 3D printing is far more prevalent in the private sector than in the government sector.
“If True Velocity can get their ammo to half the cost of traditional ammo”. The issue at the moment is that it costs double what traditional ammo does. $69.99 for 20 rounds of 308? I’ll stick with reloadable ammo thank you.
Absolutely! The price is ridiculous at the moment.
The article is very snarky about market resistance, but that resistance exists because this is about the 753rd introduction of alternatives to brass cases. From Gyrojet to consumable cases, they’ve all fallen by the wayside.
Overall, I like the TrueVelocity concept, and I hope it becomes workable. I also like that they’re producing calibers like .308, which will allow those of us with conventional firearms to try it out.
But like electric cars, until the price becomes competitive with traditional ammo I’ll have to watch the market from the sidelines.
The expensive part of this solution is the machined base insert. Induction heating rod stock should allow die forming an insert to current mass produced brass tolerance. Save the machined parts for sniper duty.
Evan though I am an avid reloader, this is the next logical step in ammunition development.
I cant wait to try the two 6.5 Creedmoor
loads.
As already stated, most don’t reload. However, if ammo prices stay high, or stock stays or becomes limited, reloading is always an option. Non-reloadable ammo takes away options. Of course options is why I shoot multiple calibers from different firearms. Bring on the innovation!
Is there a time frame on the 6.5 Creedmore ammunition and when it will be available and what weight bullet it will come in. Thanks
been keeping an eye out for this stuff for about three years or so , i have lost interest in your company and your product do to the responses ,pricing , and the stupid collector box please remove my email address from your data base
The author’s snark reminded me about Recoil’s early elitist mis-step about “assault weapons.” Freedom in America depends now upon us “mouth-breathers,” not upon load-bearing prima donnas who actually serve misanthropic globalist banksters and depopulationists. Removing the option of re-loading is not a way to woo support from Americans, but is another way of increasing the divide between us. Keep it up. You’ll get the world you deserve.
The .gov contracts have covered the R&D cost and we would expect these rounds to cost much less than brass rounds do with the extra savings being passed along to the end users. And if they really want to compete in the commercial market and take a large share then now would be a great time to make that consumer friendly move happen. You can bet that today’s shooters would reward them for the good will alone and keep the presses rolling 24/7.
They seem to be determined to price them selves out of the market.
Plentiful 5.56 ammo at 25 cents per round would make me switch in a heartbeat.
On the other hand, if the prices are high, I hope that the majority of shooters make the change. That will leave more reloadable brass for me.